Collaborative AI for Manufacturing
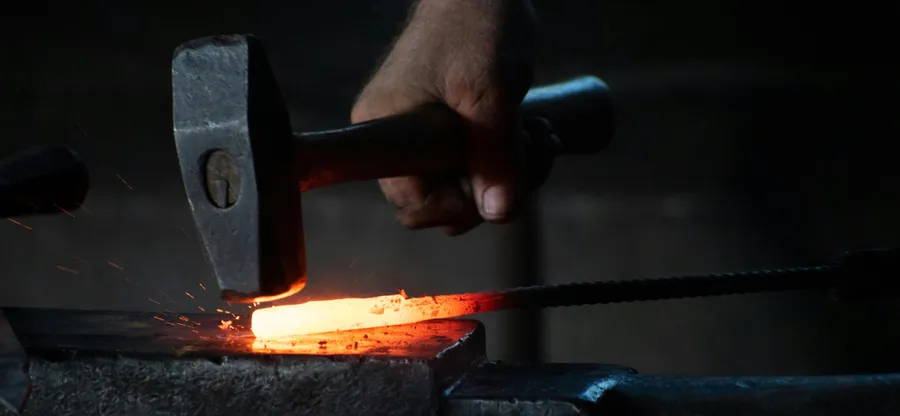
After more than two decades implementing manufacturing systems, conducting AI research, and implementing practical AI solutions, I’ve become convinced that we’re approaching a fundamental shift in how manufacturing intelligence works.
I’m currently speaking with plant managers, operations directors, manufacturing engineers, and executives about their experiences with operational data, decision-making processes, and the gap between what their systems tell them and what they actually need to know. If you work in manufacturing operations, I’d love to hear your perspective. Email me at [[email protected]].
The Manufacturing Intelligence Challenge
Traditional manufacturing taught me that the best systems amplify human expertise rather than replace it. Yet most manufacturing operations today face a paradox: they generate massive amounts of data but struggle to get timely, actionable insights when problems occur.
I’ve watched plant managers spend hours hunting through different systems trying to understand why Tuesday’s quality was worse than Monday’s, or why Line 2 consistently underperforms Line 1. The information exists—it’s scattered across production logs, quality records, maintenance data, and those critical Excel spreadsheets that somehow contain the most important operational knowledge.
What I’m Exploring
The vision emerging from my research is “Synthetic Manufacturing Expertise at Scale”—AI systems that correlate operational data in ways that would take human experts decades to learn, while presenting insights in natural language that plant managers can act on immediately.
Instead of more dashboards to monitor, imagine asking your plant: “Why did efficiency drop yesterday?” and getting an instant response like “Line 2 efficiency dropped 12% when humidity exceeded 60% while pump pressure was below 45 PSI—plants that proactively adjust pressure when humidity rises avoid this issue.”
Current Research Focus
I’m investigating how modern AI could better support:
- Knowledge transfer and retention from retiring manufacturing experts and engineers
- Natural language interfaces that let plant managers ask questions instead of reading dashboards
- Cross-plant intelligence where facilities learn from each other’s solutions anonymously
- Mobile-first design that works how plant managers actually operate—on the floor, moving between areas
- “No sensors needed” approaches that start with existing data before requiring infrastructure investment
Share Your Experience
If you work in manufacturing, I’d love to hear your perspective on:
- What questions you wish you could ask your plant and get instant answers
- How you currently handle operational problems and root cause analysis
- What operational challenges cost you the most time, money, or frustration
- Where you see opportunities for AI that enhances rather than replaces manufacturing expertise
Reach out to me at [[email protected]] to share your insights or schedule a conversation.
Why This Matters Now
Several trends are converging that make this the right time for manufacturing intelligence:
The Expertise Gap: Senior manufacturing engineers are retiring faster than they can be replaced. Plants are losing decades of operational knowledge.
Reshoring Reality: Manufacturing returning to North America needs AI-driven efficiency to compete with high-wage costs.
Technology Readiness: Natural language AI finally works reliably. Companies are actively looking for AI solutions that provide immediate ROI.
The Mobile Reality
One insight that keeps coming up: plant managers live on their phones and tablets, not at desktop computers. They’re walking the floor, responding to issues. Yet most manufacturing software assumes they’re sitting at a desk.
Manufacturing technology should work the way plant managers and their teams actually work — mobile, conversational, and immediately actionable.
Cross-Industry Applications
While my primary focus is traditional manufacturing, I’m also exploring how these concepts apply to wine production, food processing, and mining operations. Each industry has unique characteristics, but they share common challenges around operational optimization and expert knowledge transfer.
The goal isn’t generic solutions, but understanding how manufacturing intelligence principles enhance human decision-making across different operational contexts.
Background
I bring over 25 years of experience in manufacturing and technology:
- Building and implementing manufacturing systems since the late 1990s
- Two decades of enterprise software development across global operations
- Master’s degree in Artificial Intelligence with published research
- Deep expertise in manufacturing processes, quality systems, and plant operations
I’m now exploring how this experience, combined with modern AI capabilities, could create fundamentally better approaches to manufacturing intelligence—systems that enhance human expertise rather than trying to replace it.
Note: I’m not selling anything. My goal is to understand genuine operational challenges and explore how modern AI could address them in practical, valuable ways.