Why I'm Researching Collaborative Manufacturing AI
-
Nigel Browne
- Jul 13, 2025
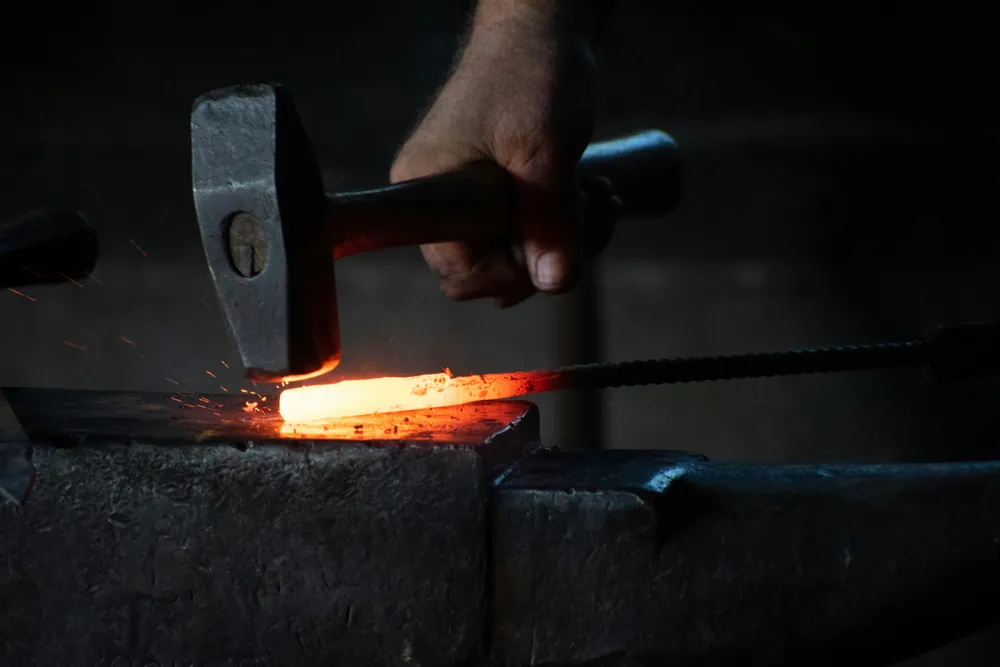
I’ve spent decades implementing manufacturing and enterprise systems and I’m fascinated by a specific challenge: how modern AI can augment human expertise in manufacturing without replacing the craft, judgment, and experience that creates operational excellence, while improving profitability and employee engagement.
This isn’t just another AI project. Manufacturing represents a unique intersection of technical precision and human artistry. While we’ve seen countless AI pilots and Industry 4.0 initiatives, most focus on automation rather than amplification. They miss the fundamental reality that the best manufacturing operations depend on decades of human expertise that no system can replicate.
Think about it - a plant manager needs to correlate data across production logs, quality records, maintenance systems, and energy usage to understand why Tuesday’s efficiency was worse than Monday’s. They need instant answers to operational questions while walking the floor, not more dashboards to monitor. And they’re doing all this while the senior engineers who hold decades of tribal knowledge are retiring faster than they can be replaced.
My research into wine industry technology sparked an important realization. Just as wineries need systems that enhance rather than constrain the craft of winemaking, manufacturers need AI that amplifies rather than replaces manufacturing expertise. Current manufacturing AI seems to force companies to choose: either invest in expensive sensor deployments that take months to show value, or use generic business intelligence that doesn’t understand manufacturing operations. Neither option addresses the core challenge.
I’m particularly interested in what I call “Synthetic Manufacturing Expertise at Scale” - AI systems that can correlate operational data in ways that would take human experts decades to learn, while presenting insights in natural language that plant managers can act on immediately. Imagine asking your plant “Why did Line 2 slow down yesterday?” and getting an instant response with specific correlations and solutions from similar operations.
This represents a fundamentally different approach. Instead of trying to automate operations, we’re augmenting human intelligence. Instead of requiring massive infrastructure investments, we start with data manufacturers already collect. Instead of creating more systems to monitor, we enable natural conversations with your operations.
The knowledge transfer crisis makes this urgent. Senior manufacturing engineers are retiring, taking decades of operational insights with them. Meanwhile, plants struggle to share best practices even between shifts. There’s an opportunity to create AI that helps preserve this expertise while making it accessible to the next generation of manufacturing professionals, in a way that serves them best.
I’m starting a research project to understand how manufacturing operations really handle root cause analysis, proactive and predictive systems, knowledge transfer, and cross-plant learning. I want to learn about peoples experiences with operational data and the gap between what their systems tell them and what they actually need to know.
If you’re interested in learning more about this research or have experience in manufacturing operations, I’ve created a dedicated research page with additional details. This represents an evolution from my wine industry work - applying the same human-centered, expertise-amplifying approach to the broader manufacturing challenge. I’ll be sharing insights and observations as the research progresses.